Making waves in the world of haptics. The future of virtual reality imagined by exiii.
Making waves in the world of haptics. The future of virtual reality imagined by exiii.
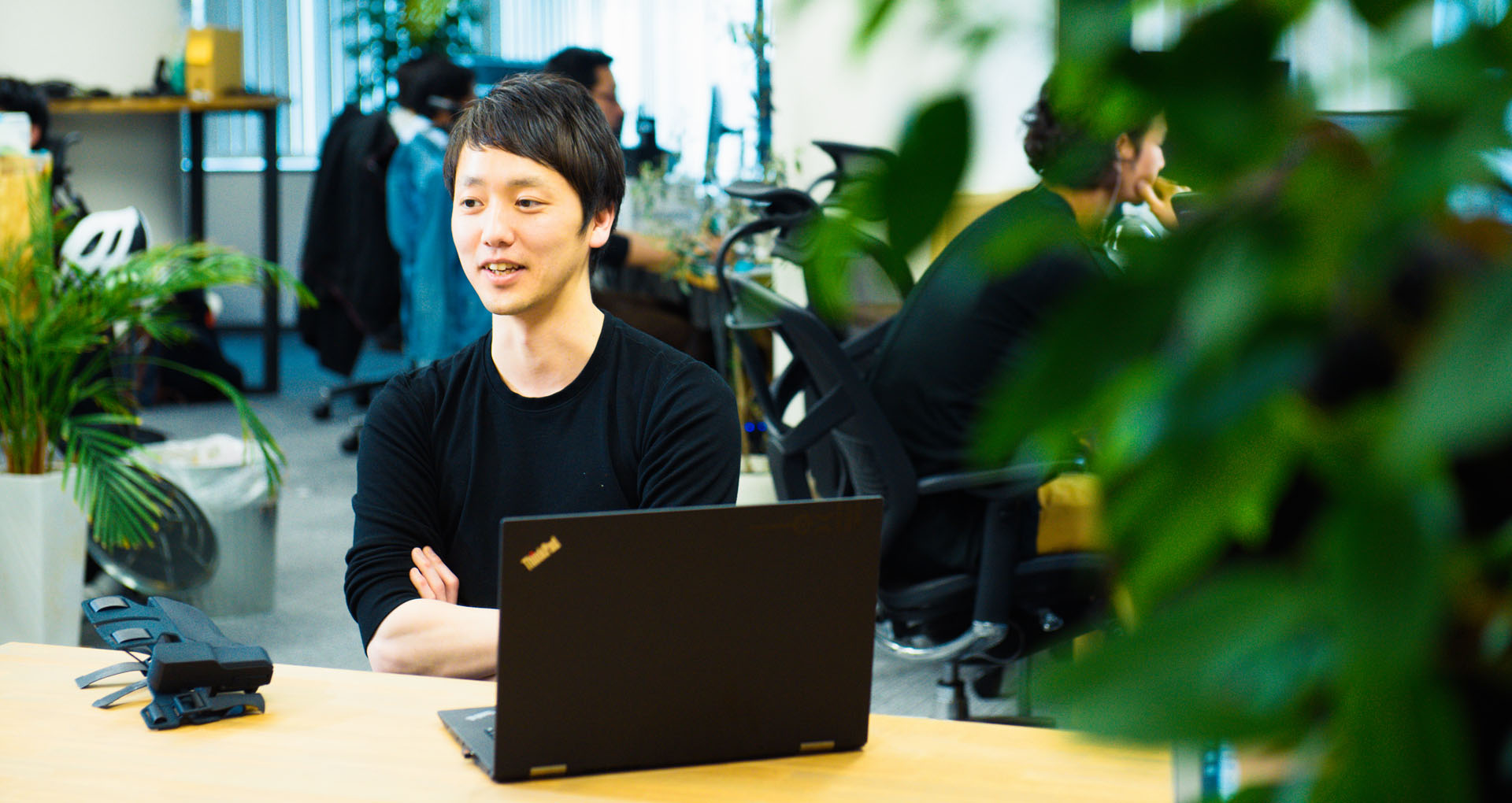
What do you think of when you hear VR (Virtual Reality)? Many people imagine a form of entertainment where you wear a headset and experience a virtual space visually. However, VR is not just a visual experience. This time, we’re interviewing exiii Inc., a company that researches and develops haptic devices for VR, AR (Augmented Reality), and MR (Mixed Reality). Haptic technology is not only for games and other forms of entertainment, but can be used broadly in development for other products. We spoke with founder and CEO Hiroshi Yamaura about the future potential of haptic VR.
EXOS, a haptic device
that gives you tactile sensation in virtual spaces.
-Thank you for your time today. I’ve just experienced a demonstration of “tactile VR”. I was astonished when I touched and moved something existing within the virtual space, then got tactile feedback for the action.
Thank you very much. What you just experienced was haptic VR, what we have been working on. When you wear EXOS, the haptic device developed by our company, on your hand, you can feel as though you are touching, holding, and grasping things in the virtual space. You can also feel as though you are moving things around and even feel textures to a certain extent.
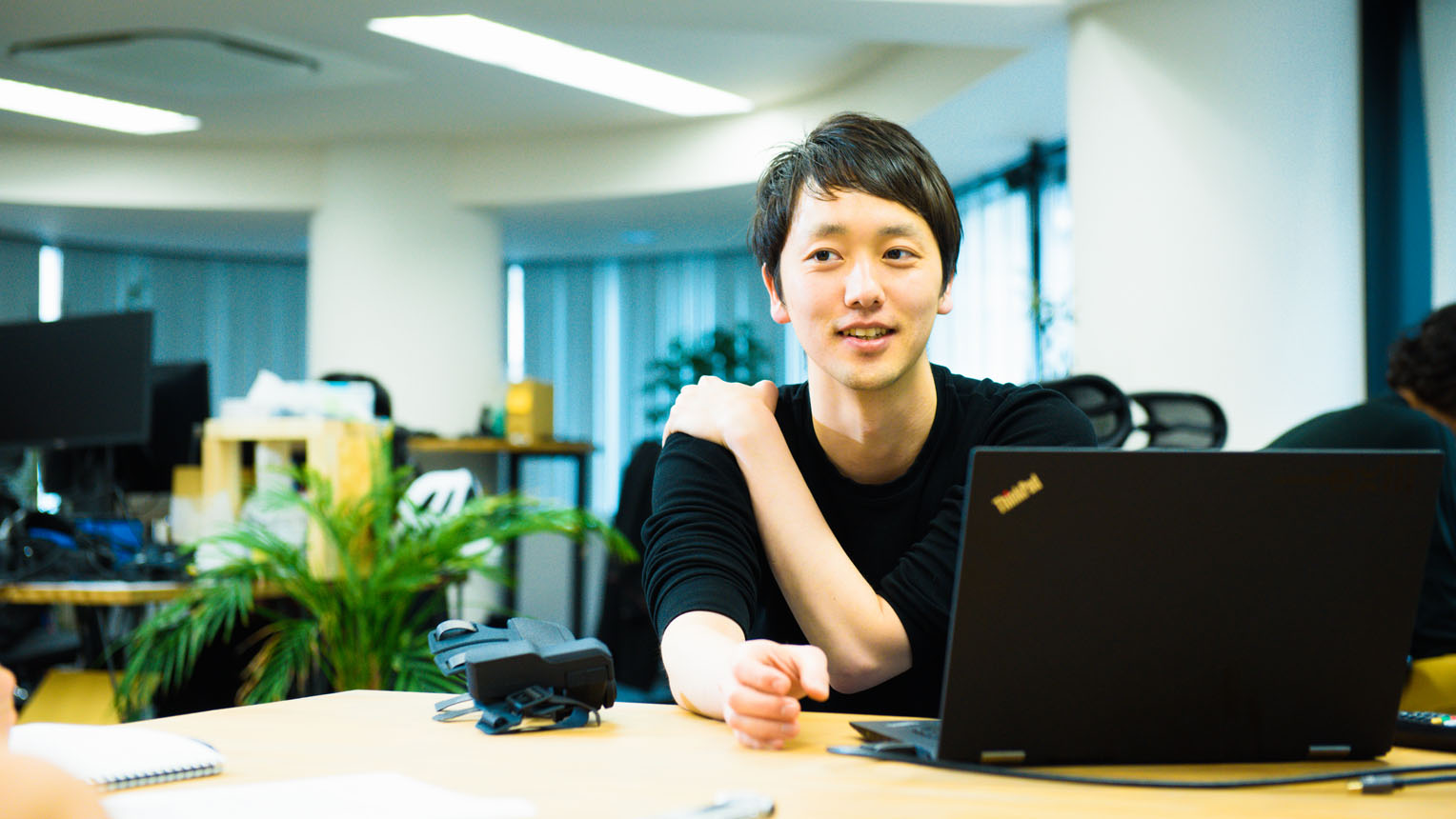
exiii CEO Mr. Yamaura
-So you’re saying that recreating touch is one approach to VR.
The current XR (a collective term for VR, AR, MR, and the like) is focused on visuals, and there has been little progress in the field of haptics. However, recreating the sense of touch in the virtual space would play a huge role in the field of B2B. One area we’re currently working on is the automotive industry, and right now creating prototypes and mockups in the automobile manufacturing process is crucial. However, making prototypes costs time and money. Using haptic VR, we could get into car in virtual reality, and use haptics to touch various parts within the car. Checks such as lowering steering wheels that are too high or changing the position of buttons that are hard to press could be done without making a mockup.
-Many people think of VR as a form of entertainment, but this technology is also drawing attention in B2B. Even so, the form of EXOS is futuristic and cool.
Thank you very much. It consists of parts pressed by the skin to produce sensation and parts that move the muscles and tendons to produce sensation, the combination of which creates the sensation of touch. We named EXOS after the English word “exoskeleton”. A shell surrounding something muscular, like the structure on a shrimp, is called an exoskeleton.
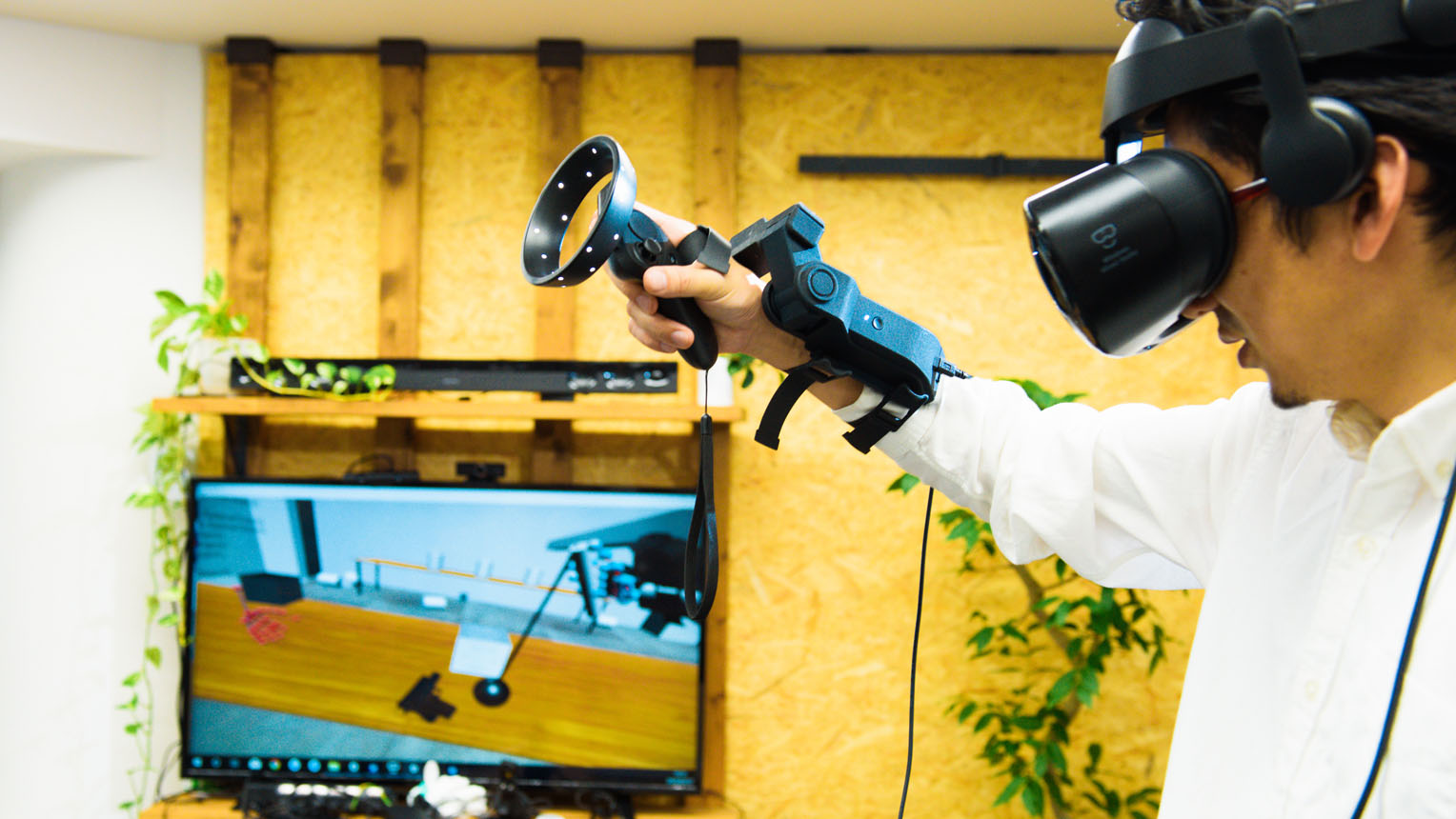
Actually wearing on EXOS and experiencing VR
-It definitely does feel like some sort of crustacean is on my arm. Did it take a lot of trial and error to get EXOS where it is today?
It was all trial and error. It underwent various changes, starting with the first EXOS printed with a 3D printer and cleanly mounted film, to a five finger type and then a two finger type afterwards, then to a pinching type.
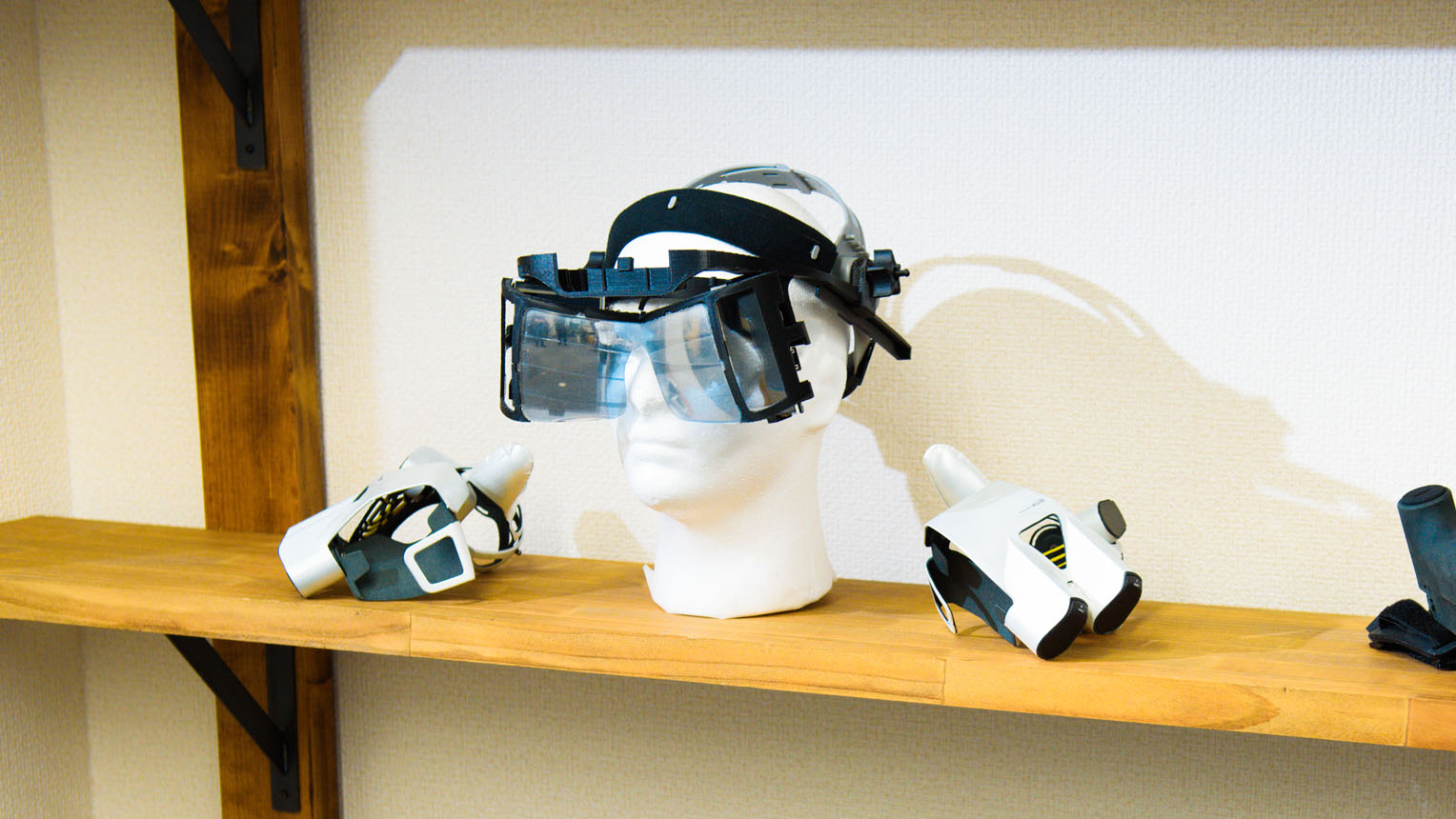
The first EXOS, something to be commemorated
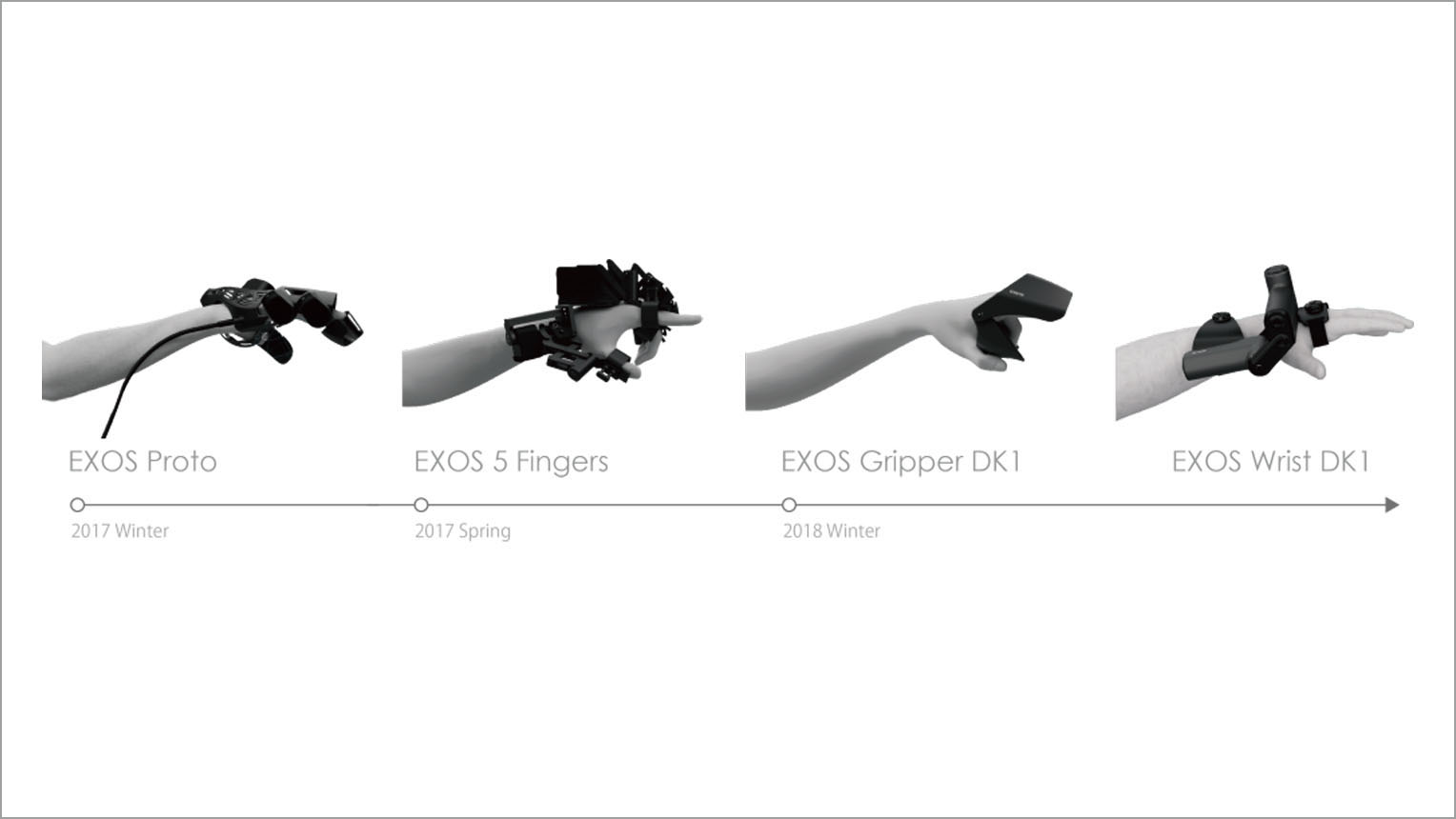
Lineage of EXOS to its current form
-Making a chronological diagram makes it look like evolution, but each with a different use and direction, doesn’t it?
Yes, each has a different purpose. The earlier EXOS had just one motor. It had one-way power, but if asked what we can do with that, there isn’t really much, is there? Everything started from here. If you want to use the device in car design and inspection, you want to be able to feel with the entire palm of the hand, but this was only the fingertips, meaning you could only get data one-way. The two-finger type makes it possible to grab something with your fingertips, but its applications are quite limited. Now, we can recreate what kind of power is applied and from what direction on the entire hand.
-Did you have any breakthroughs with all the versions you had? If so, what kind of breakthrough was it?
To put it simply, this would be making the motor and battery smaller and lighter and making communications wireless and faster. Improving these basic specifications dramatically changed the quality of the experience.
-Improving basic specifications is a big issue in development, isn’t it?
Ultimately, since this is a wearable device, it won’t work well if it’s big or heavy. If there were no limits, we could use a heavy but high-performance motor that would create something even closer to human touch. But realistically speaking, we can’t use such a thing. That is why each time, we must face the constraints of weight and capacity. The issue is how to balance performance within the constraints.
Renowned worldwide for projects outside the company.
Starting a business in pursuit of manufacturing beyond boundaries.
-Mr. Yamaura, please tell us about your career leading up to you starting a business.
I originally researched robotics at graduate school. I developed various devices in the context of “harmony between humans and machines”, including artificial hands. You could say that what we’re currently developing is based on my university research, since it is like hacking human senses.
-Why did you choose that field of research?
Many of the other machinery labs dealt with themes of very elaborate, elemental technology. Like incredibly strong materials or motors with high torque. In contrast, the theme for the lab I was in was “harmony between humans and machines”, and a field that was close to practical application that tried to solve problems using combinations of various elemental technologies. I liked creating gadgets through my ingenuity and thought this kind of practical application would suit me. Also, I heard the following at the lab: “The human body moves with great precision, and is astonishingly powerful and durable. It is extremely difficult to perfectly recreate the human body, and it could even be said that the human body is an extremely complex machine. The more you try to recreate human function through engineering, the more you’ll realize how amazing the human body is”. When I heard this content, I just thought it would be possible not only to make things, but do interesting research as well.
-After that, you worked at a manufacturer, which led to you starting your own business, isn’t that right?
Yes. At Panasonic, where I worked, I was involved in digital camera design. While I was there, I worked on a variety of projects outside the company with those who would be the founding members of exiii, one of which, a prosthetic hand, received the James Dyson Award at an international design competition. After that, I began considering starting my own company. The background for starting my business was that I wanted to make the theme I’d won an award for into a reality. Also, I wanted to work in a way that was different from how large companies worked. I can mention those two points. In the manufacturing industry, the organization is divided vertically into neat categories, so planning is for planning division, design is design, and manufacturing is manufacturing. But the fun of manufacturing lies in experiencing the entire process. Thinking about this made me interested in creating a small-scale organization.
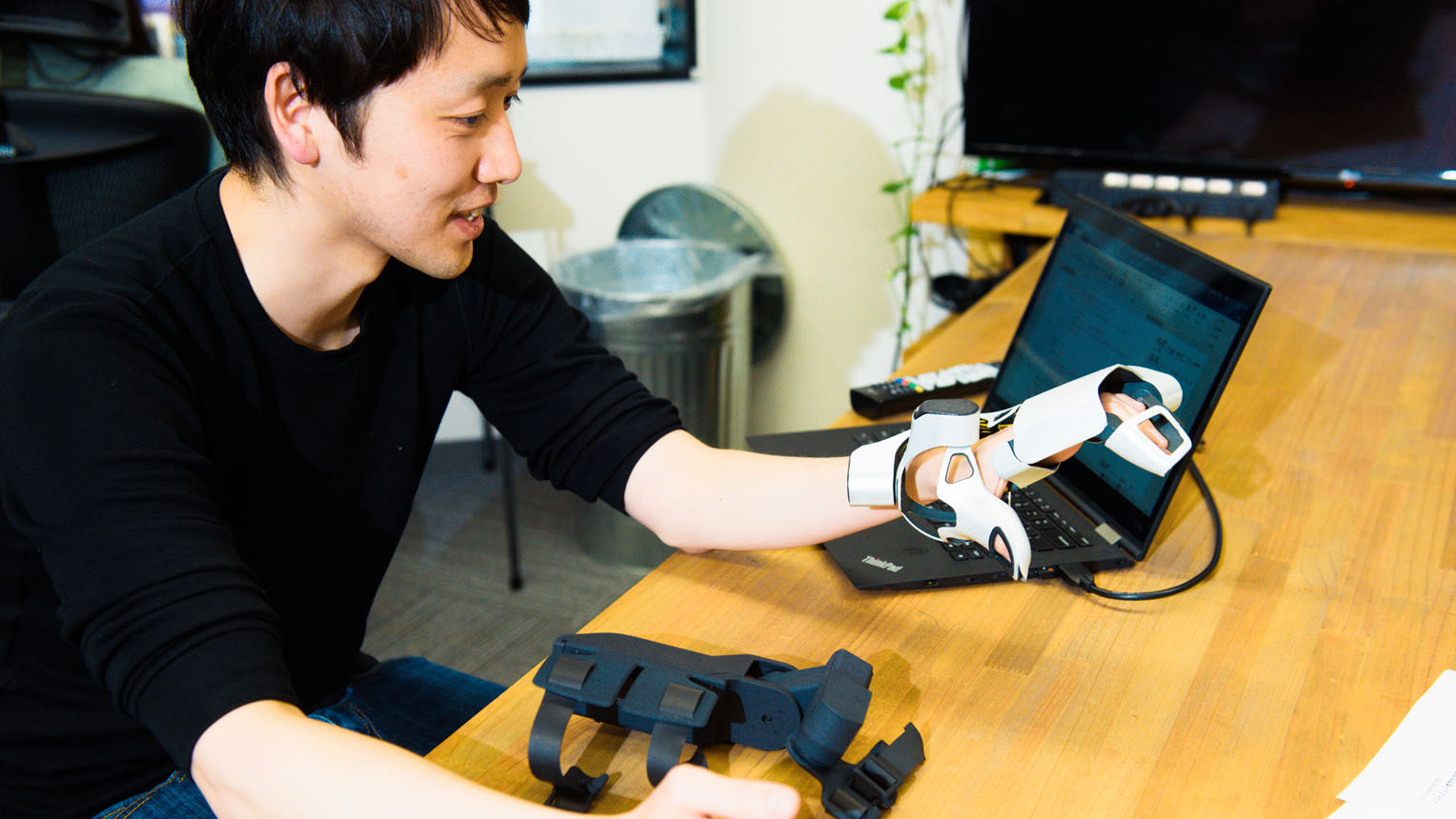
Mr. Yamaura wearing the first generation EXOS
-Were there other reasons you wanted to start your own business?
There was the fact that, in society at the time, digital fabrication was booming. That the range of what an individual could make had expanded so greatly was a huge factor. Also, this was right around the time that many hardware start-ups started appearing, and all of these companies were doing such exciting things. We saw this and thought we’d like to try it for ourselves, and that’s where we started our business.
Takes up no space, no materials costs, and no transportation costs.
What the future would be like with the haptic device XR?
-exiii’s mission is “Creating a new relationship between humans and computing”. Could you go into that more deeply?
Ultimately, current VR temporarily replaces the physical with the virtual. For example, when you try to bring a bed into your home (physical), the bed may be too big to fit. Thus placing a virtual bed down first in a virtual space lets you check whether it will fit. Then, ultimately, you bring the actual bed into the actual room (physical). When it comes to manufacturing and product development, making a prototype every time is tough, so instead we can try verifying it with VR. Then, if there’s no problem, we ultimately make the real thing. That’s how VR is currently used. However, I believe that, in the future, the ultimate use will be virtual throughout, with no physical use whatsoever.
-What do you mean by that?
For example, I think we might see such “virtual products” as a virtual piano that we can play only in a virtual space, or a cool virtual automobile that we can enjoy only in a virtual space. If we look at the piano example, there are many people in the world who don’t have enough space for a piano in their apartments. I think we could see these people playing virtual pianos as a substitute for real pianos in the future.
-Meaning they would only play the piano in virtual reality?
Yes. But that’s where the problem comes in. You see, you can’t actually touch virtual products. Current virtual pianos play sound and let you play, but there’s no sense of actually stroking the keys. If you don’t feel like your touching it, you can’t say you’re really playing it. But if you can create a sense of stroking the keys, you can solve this problem inherent to virtual products. That is why we work on haptic devices.
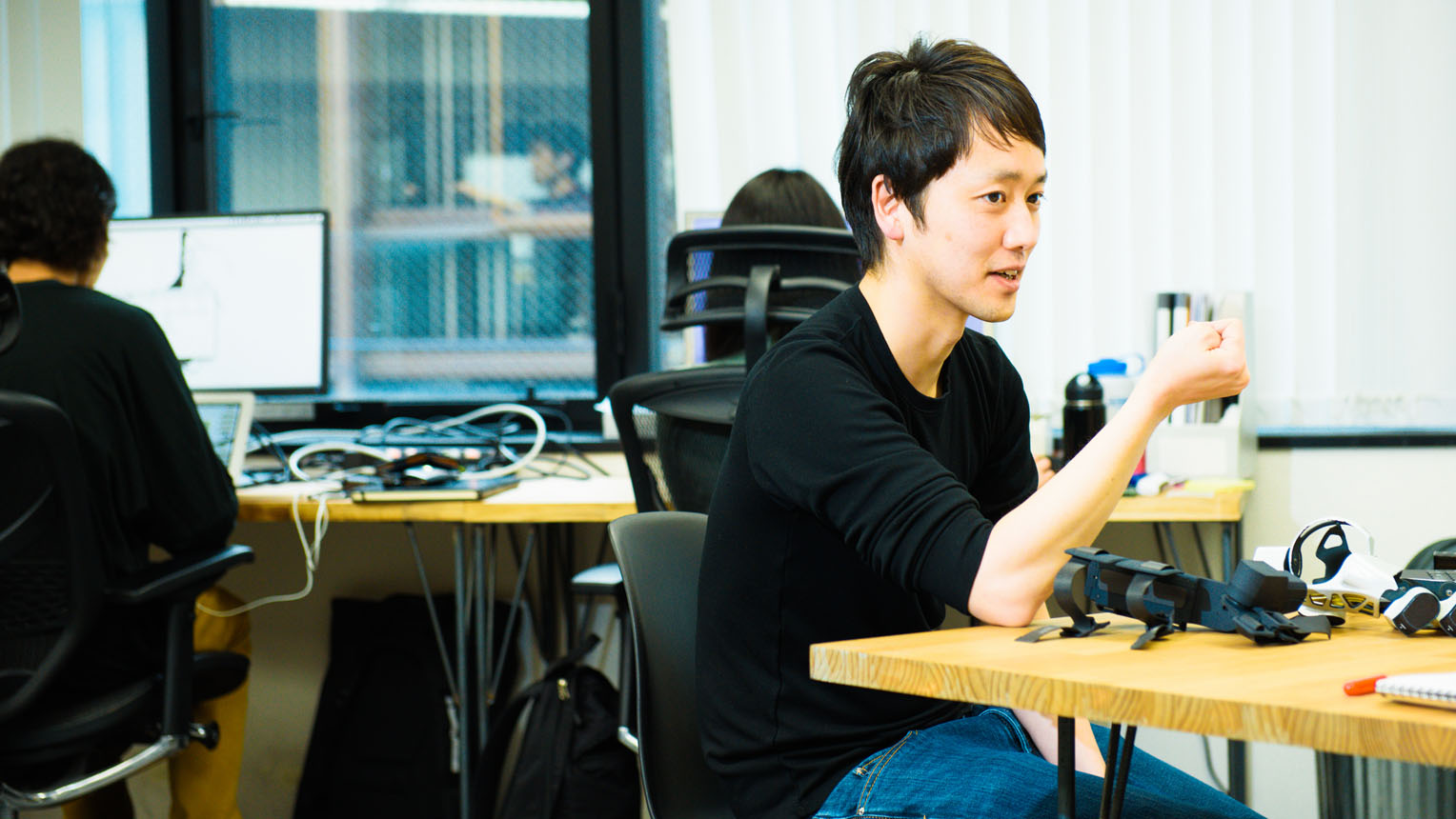
-So this is a world where objects completely in virtual reality are a part of everyday life, or in other words, “a new relationship between humans and computing”, is that right?
That’s right. Cathode-ray tube television was created about 120 years ago, and from there till now computing has been done on 2D displays. This now creates a space right before your eyes using VR, an entire space that can be used as a display. This is a huge turning point, and it is conceivable that a variety of things will be replaced by virtual substitutes in the future. TVs, remote controllers, white boards, clocks—all of these things could be virtual objects. But the big issue there is the one I mentioned a moment ago, that you can’t touch them. But if you could touch these things through haptic devices, the digital object would appear nearly the same as the physical. Virtual products will permeate our lives in the future, changing them dramatically. Such a society is included in our vision, “a new relationship between humans and computing.”
-This may be a mean question, but do you think products such as virtual pianos will actually spread to the level of daily life?
Current VR, such as the virtual piano we just talked about, are still seen as just toys. But remember the original digital cameras at the release. At first, performance was so low, they were like toys. However, digital cameras had some great features. You don’t need film, and you can check your photo right there on the spot. The fact that these features could be used was first accepted in the field, then, as performance gradually improved, digital cameras ultimately surpassed film cameras. I believe that the current virtual products are like the first digital cameras at the release. At present, performance is still low, but what is more important is that they have features that existing products don’t. For example, they don’t take up space, they’re easy to save, revise, or copy, there are no material or transportation costs, and you can extract data during use. With a piano, you could get such data as what percentage do you make mistakes at what measure and at what movement of a music score. These features don’t exist with real products, so I believe that virtual products will, like digital cameras, spread to the general population.
Expanding the future of haptic devices
I’d like to collaborate with businesses and developers.
-Is there anyone you’d like to collaborate with in the future?
exiii currently focuses on collaborations within the manufacturing industry, so if there are any companies in the manufacturing industry that could use haptic devices, we’d like to collaborate with them. Recently we deal mostly with automotive and heavy machinery, but there are many other industries haptics are suited for, so we’d like to collaborate on those areas. We’d also like to expand applications for haptic devices, so we want to work with developers who bring us interesting ideas for how they’d like to use this technology. We also offer programs to create examples of the use of our product, such as lending it to developers who want to try it but can’t buy it because of the size of the organization or for budget reasons.
-I heard there are some interesting things happening right now as well.
In terms of actual output, we have a project to learn craft skills using VR. This project to help people acquire the sensory skills of craftsmanship. For example, you can experience how, when a Japanese chef slices up fish, the fish feels as you slice it, through the haptic device.
-Craftsperson and technology, how interesting. So this recreates the actual work of the craftsperson?
That’s right. We record the field of vision that the craftsperson sees and record their arm movement and strength. Afterwards, those who want to experience it put on a headset and wear the haptic device on their arms, then they can understand where the chef is looking and in what way they slice the fish, and the arms are moved in the same way that the craftsperson moves their arms.
-This could be used to show how sushi chefs make sushi, couldn’t it? I hope companies and developers interested in haptics after reading this article get in touch with your company.
Yes. We’d definitely love to hear from them. Let’s create “a new relationship between humans and computing” together.
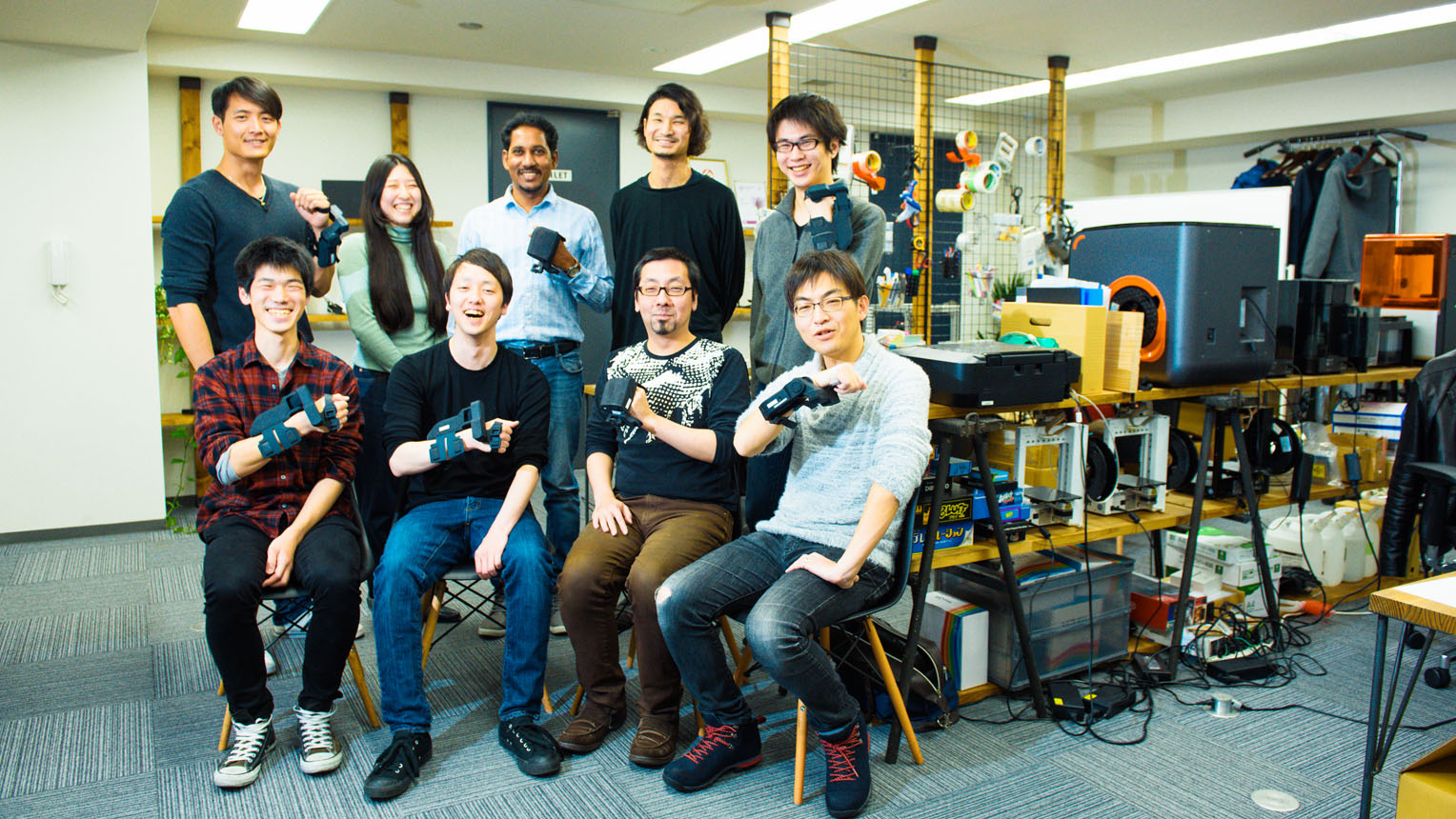
Interview/Text: Ichiro Yasui (Konel), Photo: Daisuke Okamura
exiii, Inc.
Developers of EXOS, a wrist-mounted haptic device that lets you experience touch in XR spaces, such as VR and MR. It is primarily being used in the development phase of the manufacturing industry. In the future, its use not only in manufacturing but in a wide variety of fields is anticipated.